Lavender essential oil is extracted using various models of steam distillers. Many lavender growers have relatively small distillers, which make maximizing oil extraction efficiency very important. Over the past two years OMAFRA and the University of Guelph have been testing various methods for getting the most oil out of your lavender.
Results in 2013 with a replicated research trial showed that it was better to keep some stem material on the lavender in the distiller than to try to remove all of the stems. When the distiller was filled with mostly flowers and less stems, the vessel became too tightly packed and less oil was extracted per weight of flowers. This was probably due to the development of channels through or around the flowers where steam by-passed the plant material and was unable to pick up the oils from the buds in the centre of dense areas of flowers.
We also showed a decline in oil quality through the run. The last few ml of oil had much lower quality than the first. As a result, it might be better to either stop the distillation when the flow of oil starts to slow down, or separate the last oil from the rest to be used in products where lower quality oil will not be a concern.
In 2014 we had much fewer flowers to work with due to winter damage and could not repeat the initial trial. We conducted a small demonstration focused on how to fill the vessel instead. This work will have to be repeated before we can make firm conclusions. Given that our previous study showed that stems are needed to keep the flowers evenly distributed in the vessel, we wondered what effect packing the vessel and the amount of flower material in the vessel have on the efficiency of oil extraction. The trial was conducted in a 40 L stainless steel distiller (Figure 1). The distiller was filled with various amounts of flowers packed in the vessel, and an additional treatment with the vessel full of flowers but unpacked.
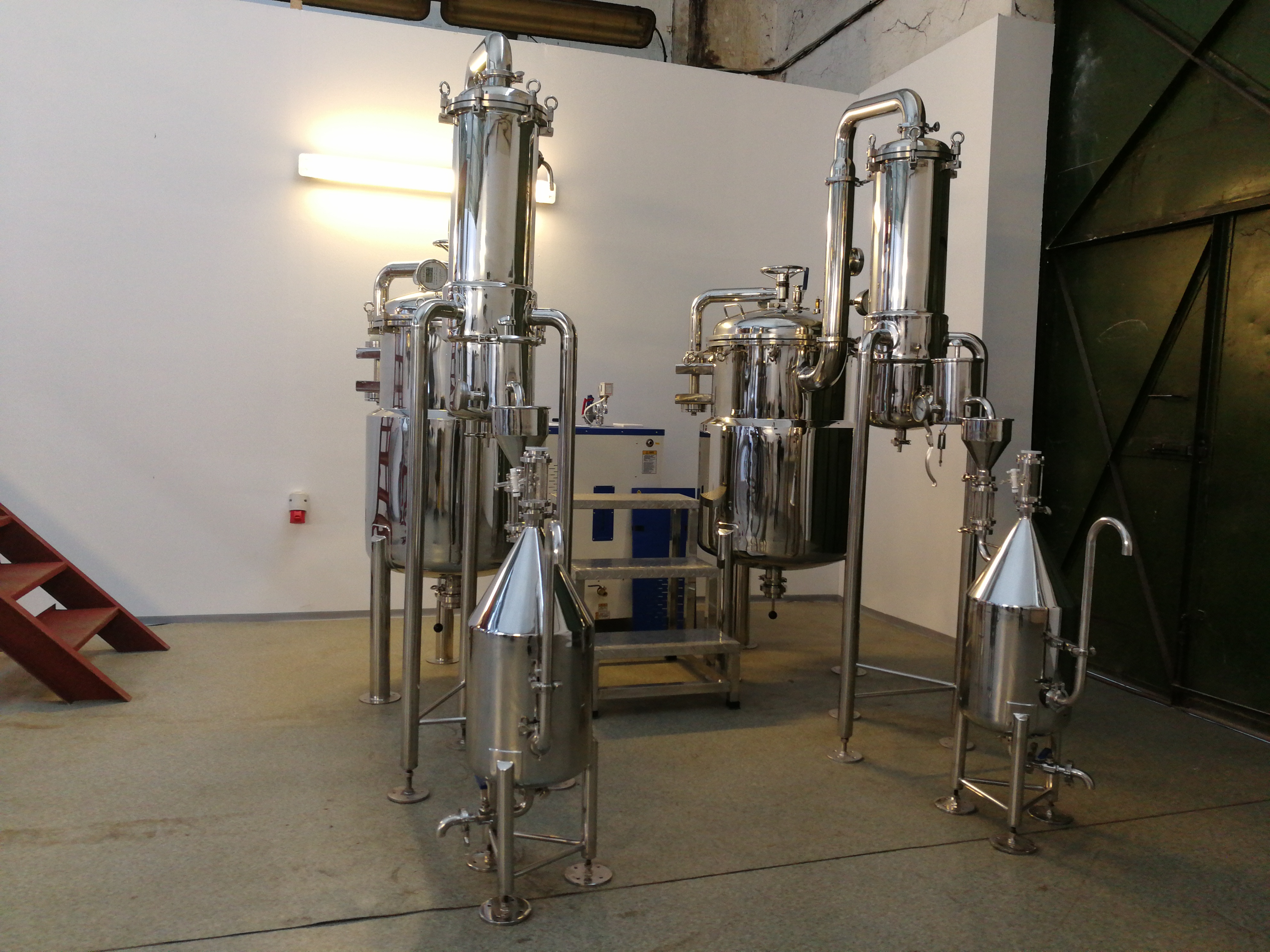
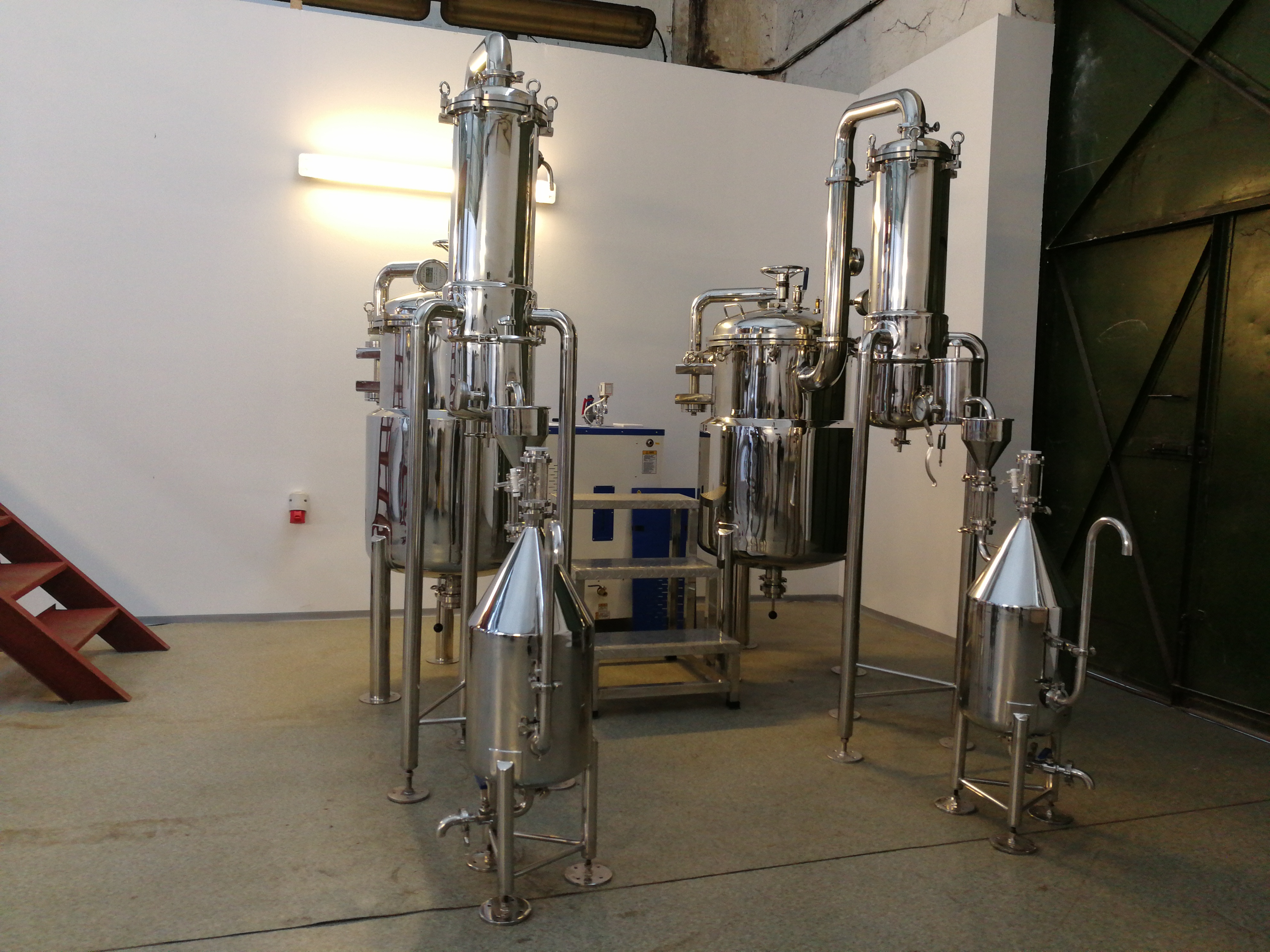
Figure 1. Stainless steel steam distiller used for the trials.
The highest extraction efficiency occurred when the vessel was full and packed (Table 1). This treatment was more efficient in both the amount of oil extracted per kilogram of flowers and the amount of oil extracted per minute. This would reduce the amount of labour required per volume of oil. When the vessel was full but unpacked, efficiency was higher than when the vessel was half full and packed with the same amount of plant material. This suggests that if the vessel cannot be filled, it is better to keep the material unpacked. If the vessel is only half full, packing of the plant material may increase the risk of channels developing that allow the steam to go around the plant material without picking up the oil. This is less of a concern with a full vessel because the depth of the plant material increase the chances that the open channels will be blocked.
Table 1. Effect of packing and amount of flowers in the vessel on lavender essential oil extraction.
Treatment | Weight of flowers in distiller (kg) | Time required to extract majority of oil (min.) | Oil extracted (ml) | Oil extracted per kg flowers (ml) | Oil extracted per minute of run |
25% full and packed | 1.46 | 30 | 17 | 11.6 | 0.6 |
50% full and packed | 2.93 | 50 | 52 | 17.8 | 1.0 |
75% full and packed | 4.39 | 50 | 73 | 16.6 | 1.5 |
100% full and packed | 5.85 | 60 | 115 | 19.7 | 1.9 |
100% full and unpacked | 2.49 | 40 | 48 | 19.3 | 1.2 |
Every distiller will be different, and results may vary with other distillers. Much larger distillers may have maximum efficiency even when half full and packed because of the added depth. Based on the preliminary research so far, the following guidelines appear to maximize oil output for small distillers:
- Lavender harvested with some stem remaining (20 cm) provides more efficient oil extraction. This also makes harvesting easier than if just flowers are harvested.
- The distiller should be filled carefully to ensure the flowers are evenly distributed during filling.
- If there are sufficient flowers, the vessel should be filled to the top and packed periodically during filling. If there are not sufficient flowers, the flowers should be kept loose but evenly distributed.
- Once the distiller is running and the oil is flowing, waiting for the last drops of oil will degrade the overall quality of the whole batch of oil. Consider separating the last 25% of the oil for use in products. The last few drops may not be worth the extra time required, since that same time could be spent starting the next run.